Introduction: The Growing Challenge of Cooling High-Performance Electronics
I came across an interesting fact when researching the evolution of cooling fans. In 1945, the volume of human knowledge was doubling every 25 years. By the end of the 21st century, it was 12-18 months. Today, human knowledge is estimated to double every 12 hours, yes, every 12 hours. The exponential rate at which human knowledge increases is driven by the two innovations, HPC (high powered computing) and the internet.
- The internet allows individuals instant access to vast amounts of knowledge. Couple this with the ability to communicate and collaborate said knowledge with individuals around the world at near light speed and you get a knowledge base that is not only doubling but is now growing at an exponential rate.
- High Powered Computing is making it possible to run real time modeling of global weather patterns, simulations of the interaction between the fundamental building blocks of matter and the forces that govern them, oh and let us not forget about Artificial Intelligence (AI), ever heard of it.
But there is a cost to such high-performance electronics, the increasing power needed to fuel the electronics industry. And power means heat, lots and lots of heat. Not only are the electronics needed for HPC and the internet getting more powerful, but they are also getting smaller and denser. This creates a challenge for thermal engineers who must balance the performance of their next generation products with the excessive heat these power-hungry devices create.
To keep these systems performing at optimal levels, the excess heat must be continuously removed. Cooling fans that produce enough airflow to remove the excess heat are a viable solution. Calculating the necessary airflow to remove the excess heat can be determined with a few simple equations. Once we know the airflow required, we can select a suitable fan. That was easy, right. Well, no. It turns out that selecting the right fan is not that easy, let’s find out why.
1. Energy Transfer: How Cooling Fans Impart Energy to Air
To start with, fans do not create airflow. A fan simply imparts energy to the air particles which accelerate the air forward. To understand this counter intuitive concept, let’s start with some basic fan dynamics. A fan converts electrical energy, (electricity), into mechanical energy, (rotating impeller). When the rotating impeller blades come into contact with air particles, the impeller imparts energy to the air particles. This energy takes two forms.
- Kinetic energy,
- Referred to as KE moving forward
- It is the velocity component of the air molecules
- KE =
- Potential energy,
- Referred to as PE moving forward
- PE is the pressure =
- PE is energy stored in the deformation of the air molecule.
To get a more intuitive understanding of how the mechanical energy from the rotating impeller is imparted to the air molecules, let’s look at a golf analogy.
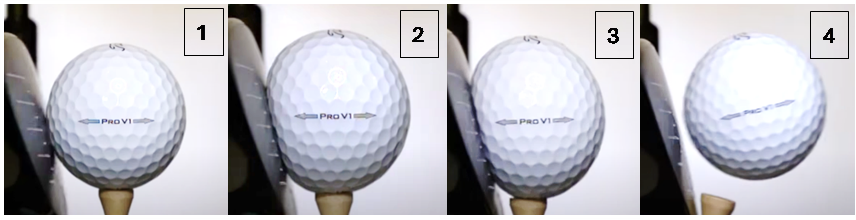
A rotating golf club imparts energy to a golf ball in the same way a rotating impeller imparts energy to an air molecule. The below three picture frames help illustrate this point.
Frame 1 – The moment right before the rotating golf club impacts the golf ball; no energy has yet been transferred to the golf ball. Therefore, there is no rotation, no plastic deformation, and no acceleration of the golf ball.
Frame 2 – Contact is made, the golf ball immediately begins to compress as the swinging golf club imparts energy to the ball. This energy is at first stored as PE in the elastic deformation of the ball.
Frame 3 – The ball continues to deform as more energy, imparted by the golf glub, is stored as PE. The ball also begins to accelerate forward as KE is imparted to the ball also.
Frame 4 – The PE stored as elastic deformation of the golf ball is converted to KE as the ball “snaps back” to its original shape, contributing to the balls forward motion. Since all the energy imparted to the ball by the rotating golf club is now in the form of KE, the ball is at its maximum speed.
One item this analogy is not able to illustrate; the distribution of KE to PE imparted by the golf club will not change each time the ball is hit assuming the velocity of the swing does not change. We will re-visit the distribution of energy topic later in this paper.
So far, we have discussed how a stand-alone fan creates airflow. To understand how to select a suitable fan for a particular application we must understand how the air actually flows in both free air and impeded air.
The importance of the energy carried by an air particle will become more important when we discuss the dynamics of airflow. For now, let’s take a closer look at how fans create airflow.
2. Pressure Gradient: The Force Behind Continuous Airflow
An engineer will tell you that a fan creates a pressure gradient, not airflow. The pressure gradient causes air to flow from the region of high pressure to the region of low pressure.
If the pressure gradient is responsible for the airflow a fan produces, then we must understand how a fan creates a pressure gradient and how the pressure gradient creates air particles to continuously flow.
I. No Rotation
Prior to rotation, the air particles are in a state of equilibrium. The density of the air particles, and therefore the air pressure, is uniform. There is no pressure gradient and therefore no airflow.
For the ease of illustration, the molecules in the path of the fans impeller have been highlighted yellow for ease of illustration.
II. Rotation
As the fan begins to rotate, the impeller comes into contact with the yellow air molecules in the path of the impellers rotation. This accelerates the air particles downstream, as illustrated below. This is a burst of air, not airflow.
The movement of the yellow particles downstream has upset the equilibrium. The air density downstream, and therefore the air pressure, is no longer uniform. A pressure gradient has formed between the atmospheric air pressure upstream and the lower pressure (vacuum) within the fan, see below figure 1.
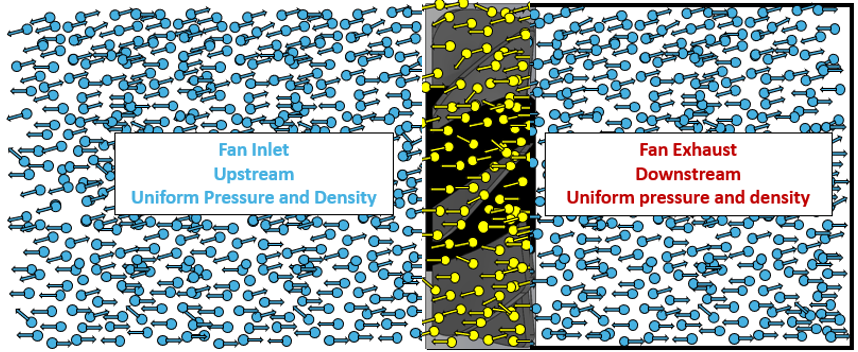
The pressure gradient effectively forces the upstream air to “reload” the fan, see
figure 2 below. Without this pressure gradient forcing air into the fan each time the fan impeller expels the air within the fan, we would not have airflow. This is how the pressure gradient, not the fan, creates continuous airflow.
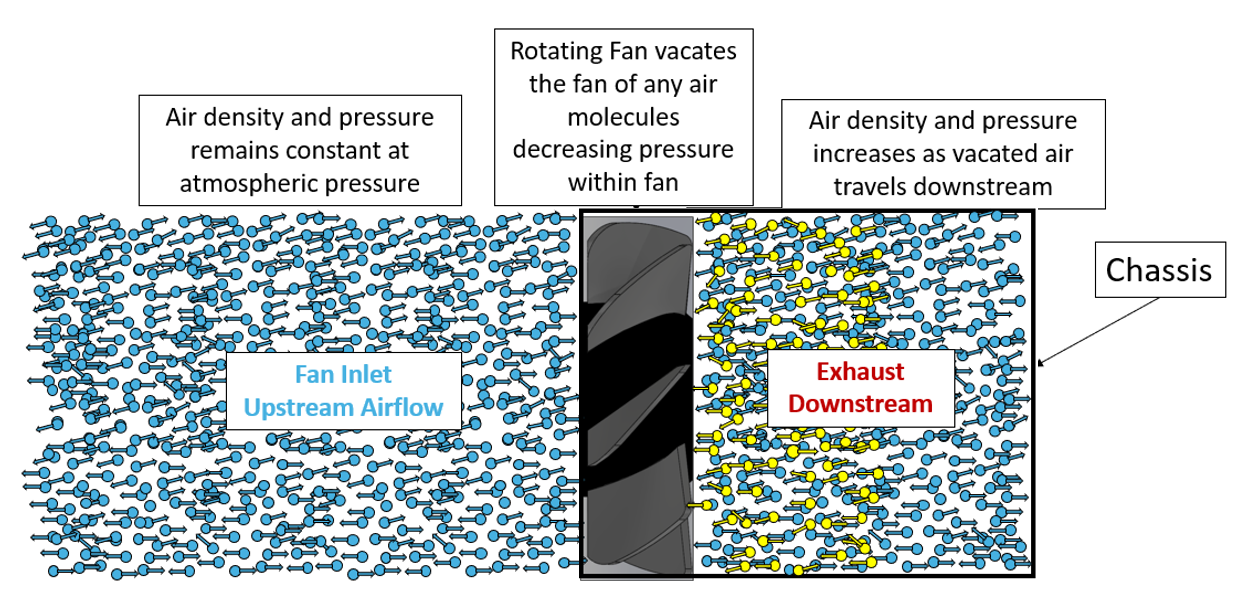
The pressure gradient effectively forces the upstream air to “reload” the fan, see figure 3. below. Without this pressure gradient forcing air into the fan each time the fan impeller expels the air within the fan, we would not have airflow. This is how the pressure gradient, not the fan, creates continuous airflow.
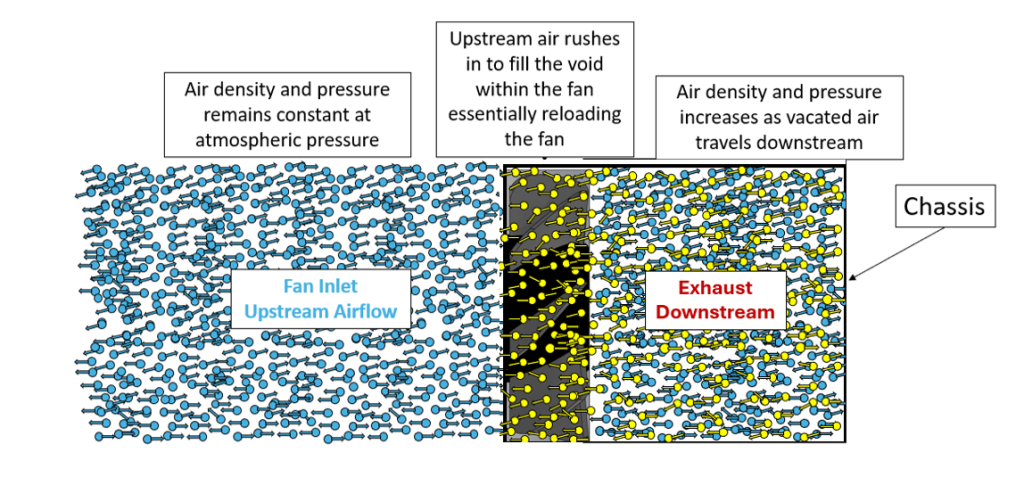
3. Airflow Dynamics: Free Air vs. Impeded System Performance
I. Free Airflow
Fan specifications list the parameters of a fan’s performance in a “free air” condition. Free air refers to air which flows without any external forces or restrictions acting on the air as it moves forward.
The air is allowed to flow freely because there are no obstacles to redirect the air or restrictions to slow the air velocity. All the KE imparted to the air by the rotating impeller is used to propel the air molecule forward. So, the SANYO DENKI fan, 9HV0912P1G001, listed in the table below will only produce 180 cfm when tested in a free air condition.
II. Impeded Airflow
In the real world, fans are designed into confined spaces with components that interact with, and resist, the flow of air. As the rotating impeller continues to accelerate air particles downstream the air accumulates due to a slowdown in the airflow velocity. The decrease in velocity is a function of the system’s impedance. The system impedance is a measure of the resistance to airflow within the system and is based on the density of the system architecture itself. Density refers to the ratio of components to free space in the system. The more impedance a system has the lower the CFM the fan can produce. The 9HV0912P1G001 fan has the ability to produce 180 cfm in free air, however, would produce less than 180 cfm through a system with impedance.
III. Here’s How it works
As the air particles flow from the inlet to the exhaust of a system, they collide with the various components in the path of the airflow or a forced to flow through constricted paths.
Each interaction causes the particle to convert a portion of its KE into heat, sound and pressure loss. As the particle loses its KE its velocity slows and the distance it is able to travel shortens.
As the rotating impeller continues to accelerate air particles downstream the density of air particles increases and the air particles begin to compress as they convert the KE of the oncoming air into PE in the form of compression.
Compression begins to occur as the PE of the oncoming air is stored by the downstream air as compression. This is similar to the deformation of the golf ball earlier. As the KE of the golf club was imparted to the golf ball, it was initially stored as deformation in the golf ball..
But there is one major difference.
The golf ball was immediately able to convert the PE into KE which continued to push the golf ball forward.
However, because the impeller is continuing to push additional air downstream the density of the air continues to increase and the air particles are forced to hold the PE stored as compression. They do not release the PE as the golf ball did, The compression is known as back pressure because, not only are the particles trying to release the PE downstream in the form of acceleration, they are also trying to release the PE upstream. This pressure exerted by the compressed air in all direction is known as back pressure because the compressed air is pushing back on the oncoming air.
As the density of air continues to grow relative to the density upstream the back pressure beings to propagate backward towards the fan.
Eventually the rotating fan blades feel the pressure exerted by the thickening air in front of the rotating blades.
The back pressure increases until the fan can no longer push air particles forward. The pressure at which the fan can no longer push air forward is the static pressure because the air is no longer moving. This is a key parameter listed on the fan specification.
The fan mentioned earlier can create a maximum of as a 4.42 in-H20 of back pressure . Since the fan can no longer push air forward it is no longer producing airflow at 4.42 inches H2O.
4. The PQ Curve: Visualizing Fan Airflow Under Pressure
As mentioned earlier, impedance is a characteristic of a system’s architecture. The level of impedance within a system determines the amount
of airflow a given fan can move through it, indicating that airflow is a function of this system characteristic. Based on this relationship between airflow and system impedance, the performance of a fan is commonly characterized by its Pressure-Flow (P-Q) curve. This curve graphs the static pressure the fan is capable of developing across a range of airflow rates.
Each point on the curve references the airflow resulting from the impedance a system has. This point is known as the operating point within the system. Different fans produce different amounts of back pressure therefore a PQ curve is specific to a specific fan in a specific system. A fan which can produce more/less pressure will be able to produce more/less airflow in the same system and will have a different PQ curve. Essentially the PQ curve tells us how much airflow a fan can continuously produce given the back pressure created by a system impeded.
Conclusion: Optimizing Cooling Fan Selection for System Design
A typical fan has a limit to how much back pressure it can handle while still pushing air forward. This limit is defined by the fan’s static pressure rating. Once the back pressure exceeds this rating, the fan blades can no longer push air forward effectively.
That is why understanding the relationship between back pressure and airflow is critical when designing a fan into high performance systems. As the back pressure increases, due to design decisions which impede airflow, the fan’s ability to maintain its designed airflow decreases. This drop in airflow not only reduces cooling efficiency but can also increase the fan’s power consumption because the fan must work harder to rotate at a constant speed.
By accounting for these effects early in the design phase, engineers can better match fan specifications to system requirements, ensuring the system is able to run at its optimal performance.
Written by Daren Perez
To learn more about PQ Curve, reading the blog “How to Understand PQ Curves By Different Cooling Fan Types” is recommended.
About SANYO DENKI
SANYO DENKI has been a trusted provider of cooling solutions for various industries, with fans being a crucial component in many advanced devices. Contact us for a quote, or to discuss your device's customization requirements.
Our experienced application engineers and field engineers will provide support on the customization or any other technical support for your equipment. Contact our representatives or distributors to start discussing your next project.
Contact Us